konwerting
Converting is a complex process of modifying raw, original material to obtain a finished product tailored to a specific application or order. The service also includes combining various raw materials to create a product with innovative and unique properties. Converting is the art of adapting adhesive materials, e.g. technical tapes, to individual needs and specifications, in line with the customer's expectations.
© 2024 cvgswhat is converting service
Determining the project requirements Based on the analysis of the customer's needs, we determine the detail specification
Suitable raw material is the basis of any successful converting project
The method of die cutting the material influences the final properties of the product.
our products for converting
- foams and technical materials
- single-sided adhesive tapes
- double-sided adhesive tapes
- technical adhesives and dispensing systems
Do you need a different type of solution for your industry?
Discover the range of our productsfeatures of converting products
The key feature of converting is the adaptation of products to specific customer requirements and expectations. It provides die-cut products tailored to market needs.
Converting products are versatile and fulfill a variety of functions, which allow for optimal use of products in different industries. In addition to improving functionality, converting enhances the aesthetics and durability of the products.
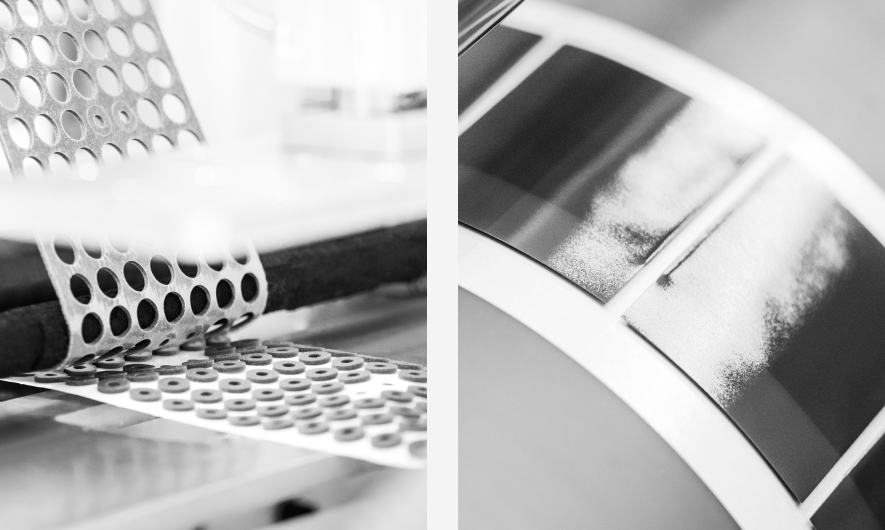
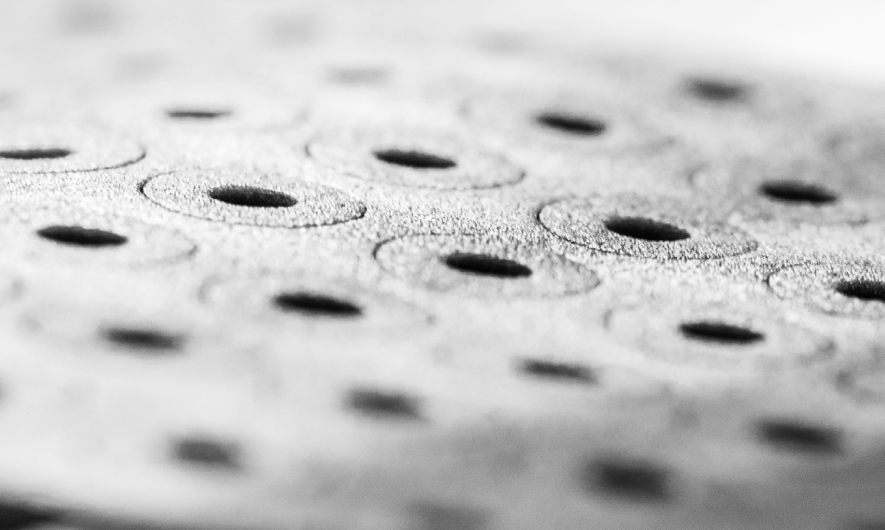
why us
We work with customers from all over the world with an individual approach tailored to each customer's unique needs. We offer a diversified service and product range and therefore our solutions meet the requirements of many industries, e.g. automotive, glass, home appliances.
With our state-of-the-art machinery park of 7000 m2, we are able to optimise the services we provide to our customers, including technology upgrades in line with their growing needs and the increasing number of new applications of our products. This confirms our leading role in the converting industry both at national and at international level.
In the lab we are able to control the amount of pollutants in the air, as well as the parameters such as humidity, temperature and pressure. Here we manufacture products requiring a high level of cleanliness.
Each project is handled by a designated consultant, acting as a main point of contact for the customer. As a result, orders are processed efficiently and in a timely manner. The team includes employees from the production, quality control, logistics and an account manager.
Together with our customers, we create projects that meet their requirements. Based on the customer's assumption, we design a solution with regard to both function and material.
Our suppliers have at least ISO 9001 certification. This ensures not only high quality, but also stability of materials.
We test both the raw materials and the finished product with reference to the supplier's specifications and the customer's requirements.
We are the only company in Poland that provides products according to ISO 8 requirements.
Timely order processing is our priority. Thanks to advanced logistics, a professional team and efficient management of production processes, we are able to achieve a result that we can be proud of - figures for 2023.
In 2023, we had only a few orders subject to the complaint process, which confirms our commitment to providing products that meet the highest quality standards.
meet ours representative
Our sales support specialist will answer your initial questions and direct you to the right consultant.
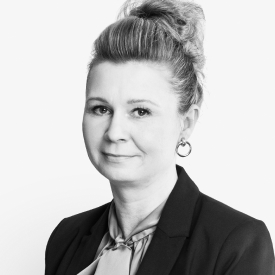
Case study
Car door seal peeling off
Problem
A customer reported a problem with a car door lock seal peeling off. The seal made of PVC foam was installed at the last stage of production.
Analysis
After conducting a detailed analysis of the assembly process, we found that the main cause of the problem was the grease on the metal surface where the seal was mounted.
Solution
We proposed to use a die-cut piece of masking tape, which was to be applied to the metal component at the first stage of the process. The tape was intended to protect against contamination, eliminating potential adhesion problems. The tape was removed before the seal was applied, which ensured a clean and prepared surface for assembly.
Result
By using the proposed solution, we completely eliminated the potential greasing of the detail during the process. The seal was mounted without any problems and the poor adhesion was effectively solved. With the new approach to the assembly process, production ran smoothly, eliminating disruptions related to the adhesion problem. A thorough analysis of the problem and the use of an innovative solution allowed us to successfully solve the problem of seal adhesion. Industries we support
industries we support
We optimize our solutions and products, and adapt them to the specific challenges that different industries face. We treat each project individually, considering the unique requirements of a given market sector.
We deliver
solutions for
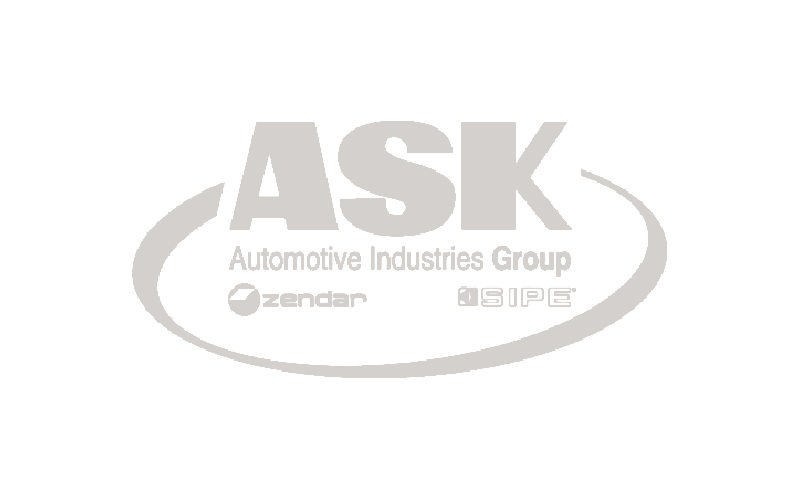
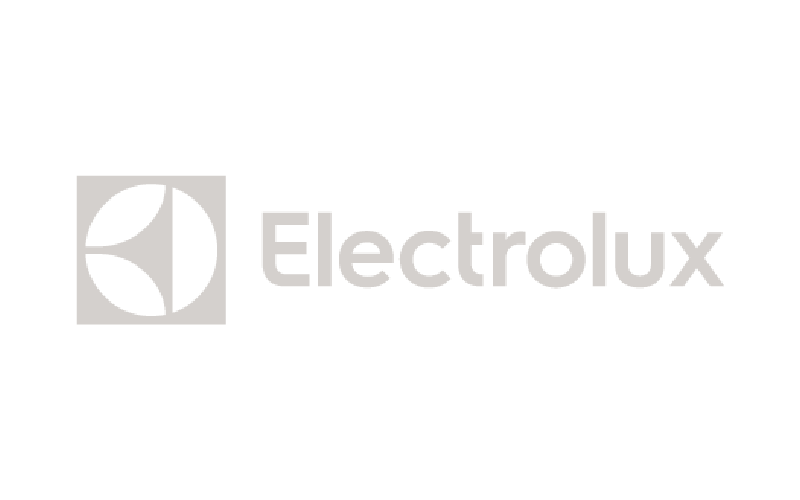
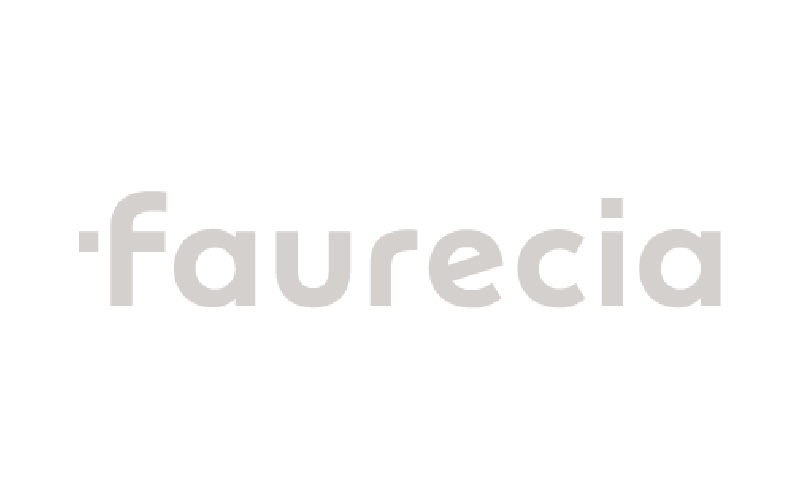
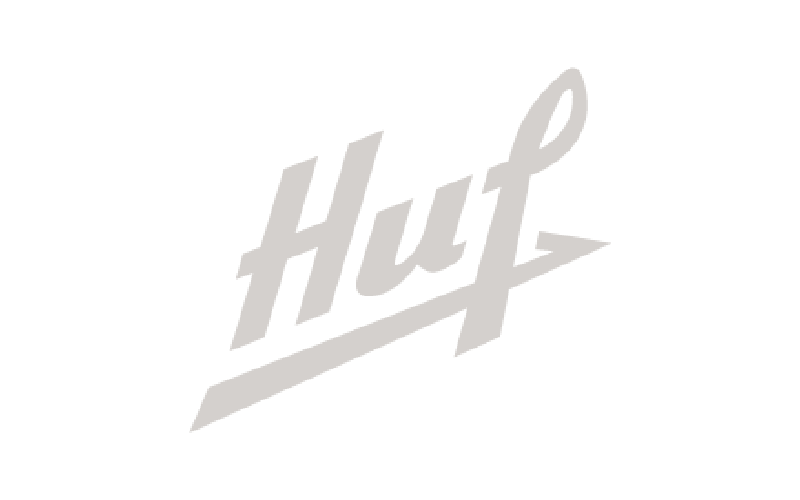
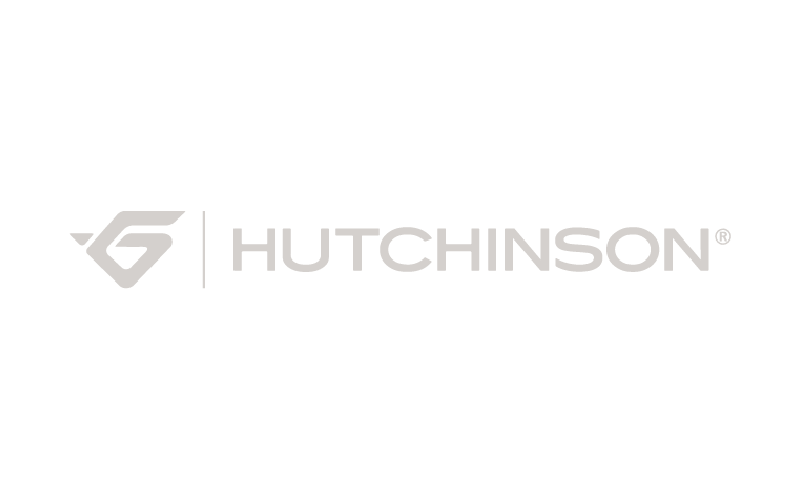
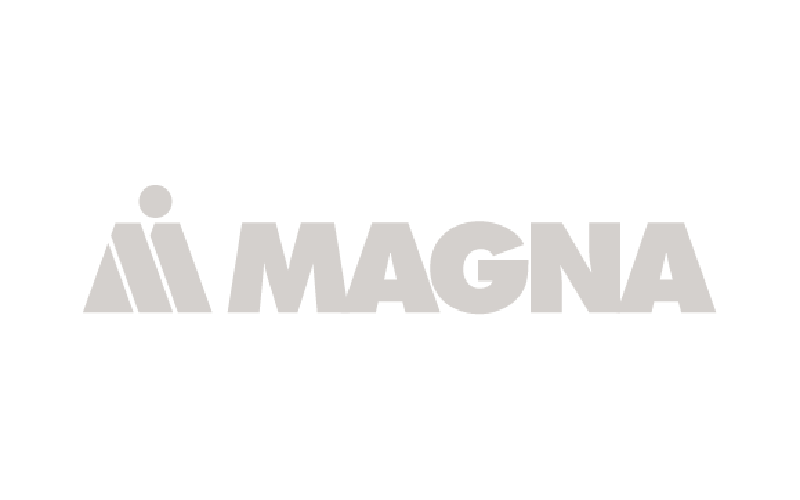
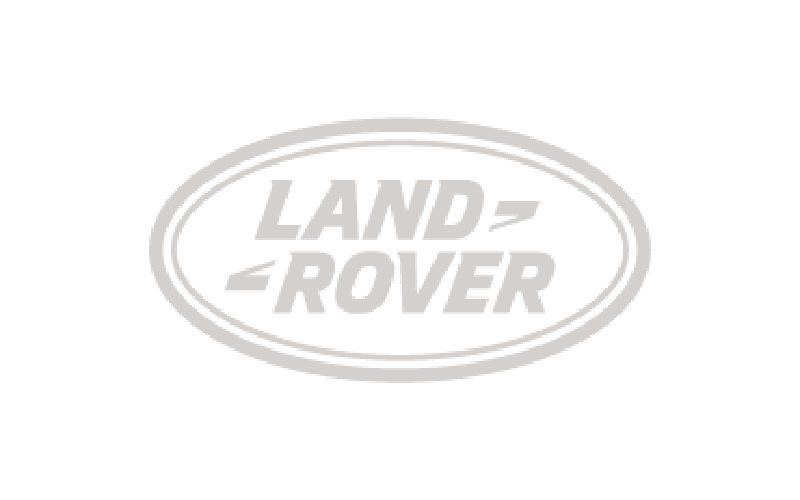
contact
with us!
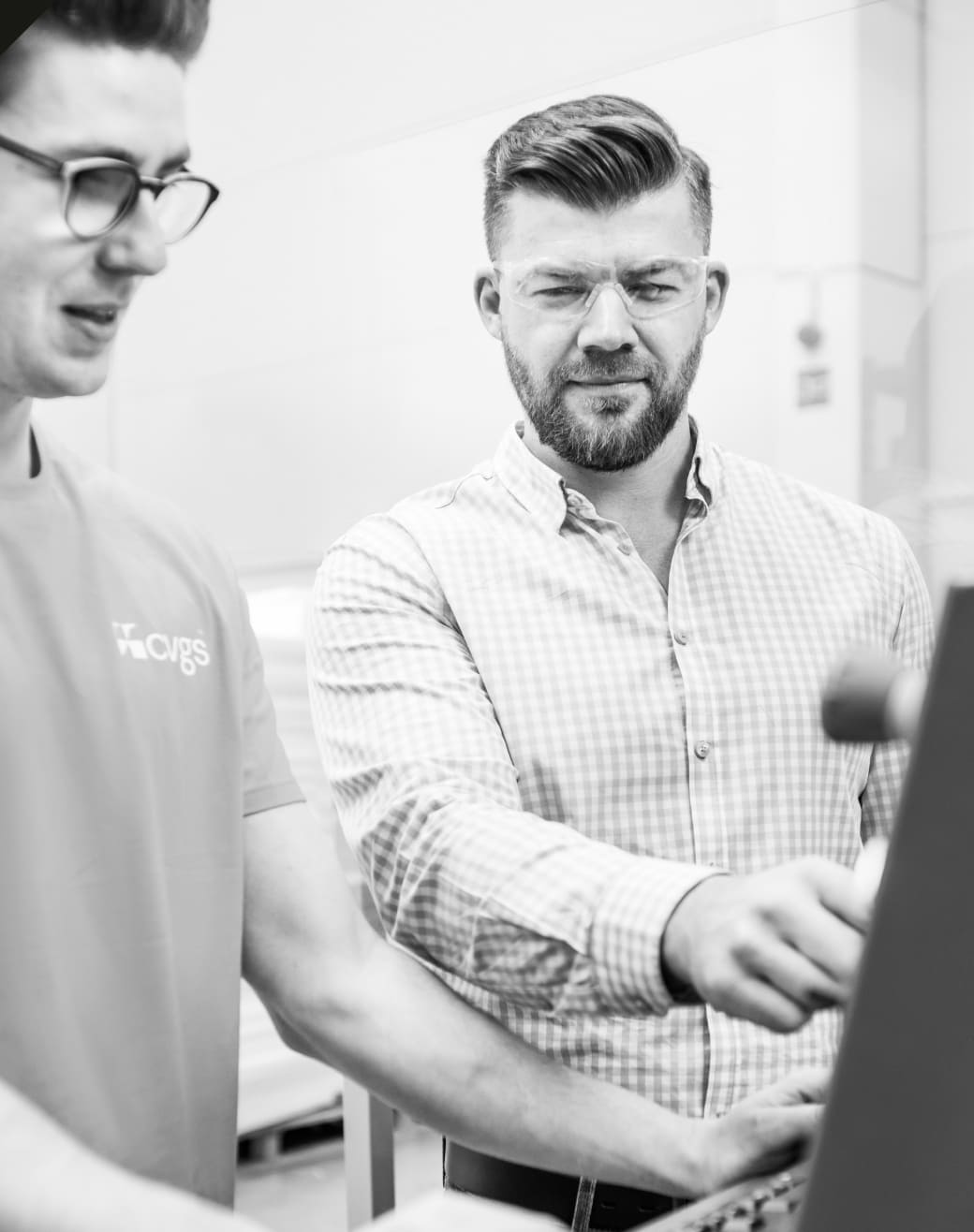
Consider what you would like to know during the consultation and fill out the form:
Our representative Anna Kuś will contact you within 15 minutes to arrange a meeting.
Let us know what products you would like to evaluate and fill out the form:
Your inquiry will be redirected to a sales representative who will contact you on the same day.
Product samples will be sent within 3 business days.
The offer will be prepared within 7 business days.
Do you know what solution you need?
Ask about the specifications of a specific product.
Our representative Anna Kuś will contact you within 15 minutes to arrange a meeting.
Do you need to consult the project in terms of quality? Do you need to find out what standards we work with? Are you looking for a converter that conducts specific material tests?
Your inquiry will go to the quality department, which will contact you as soon as possible.
Do you want to cooperate with us as a supplier or partner in another field?
Your inquiry will go to the purchasing or administration department.
We will contact you as soon as possible.
Your inquiry will go to the purchasing or administration department.
We will contact you as soon as possible.
Your inquiry will go to the administration department, which, depending on its content, will redirect the form to the appropriate department.
Download the catalogue
Do you want to get more information about our company, products or services? Just provide your e-mail address and we will send the cvgs company catalog to it!